One of the major challenges in steel production is to increase the quality of steel and reduce unnecessary waste due to cracks. To help Uddeholm, a leading steel producer, overcome this challenge, we developed a powerful machine learning-based solution that helps to identify production errors, refine processes and improve profitability.
Founded in 1668, Uddeholm is a Swedish multinational producer of high alloyed tool steel for electronics and automotive customers. The company exports 95% of its products to the international market.
By evaluating the possibilities of new technologies like artificial intelligence and machine learning, we started helping Uddeholm tackle one of their most pressing challenges: ensuring a high-quality steel product.
Cracks in steel impact profitability
Steel manufacturers cannot assess the quality of their output until the end of the manufacturing process, at which point they can discover cracks in a large amount of the finished product. The damaged steel must be melted and fed back into the process, wasting enormous amounts of energy, time and money.
Uddeholm wanted to improve their manufacturing process and reduce cracks in completed steel to avoid significant costs and wastage. Even with an abundance of data, they were unable to make the best use of it to achieve their goals, including:
- Increasing the quality of steel
- Reducing unnecessary waste due to cracks in completed steel
- Identifying key factors causing cracks
- Modifying the production process to eliminate or reduce quality issues in a cost-efficient and timely manner

These models and algorithms offer new possibilities that can take things to a whole new level. We see machine learning as integral to keep moving forward.
Head of process development, Hot work at Uddeholm
Predicting cracks in steel with over 70% accuracy
Together with Uddeholm, we developed a high-powered machine learning model that could predict—with over 70% accuracy—where and when cracks would occur.
We selected three steel products, data sources and analysis methods to analyze Uddeholm’s data as it related to quality and relevance. Our approach used big data and an Internet of Things (IoT) platform to capture and handle relevant data and apply machine learning and advanced analytics to find new insights and gain the necessary knowledge to improve the quality of completed steel.
The results, findings and insights were presented in a well-structured and visually easy-to-follow report.

Better processes, less waste
Analyzing the data and reverse engineering of the machine learning models enabled Uddeholm to pinpoint the cause of quality issues, significantly improving the ability to eliminate or reduce damaged steel. Uddeholm is now able to adjust its manufacturing process to reduce the waste associated with cracked steel.
This project is an important first step toward digitizing their steel manufacturing production process and business.
Investing in the future with modern technologies
To ensure better control over where materials are located and optimize transportation and handling, our experts also helped Uddeholm implement satellite technology to track and manage internal transportation. We are also exploring the use of 5G networks to support the steel maker’s digitization journey.
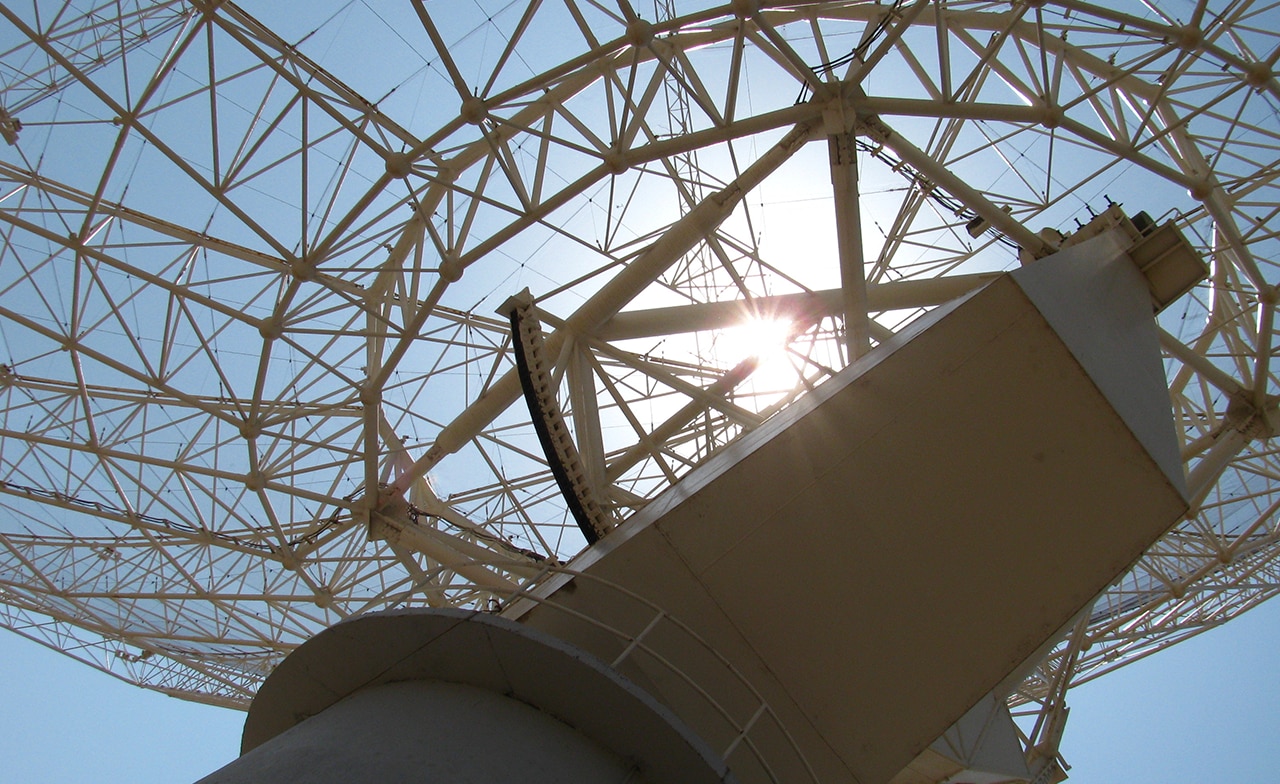